Applications
Rejecting and Depositing Conveyor Systems
Why Is Rejecting Necessary?
Rejecting is a necessary step in any production line to help increase the quality of a business’ output. Not all products are fit to be sold in a marketplace, with some estimates putting 2 percent of output as rejected parts.
Products may be rejected by sight for reasons such as an irregularity or deformity. They may be rejected because of improper weight or missing caps, flaps or labels as well as because of incorrect or unreadable barcodes. Products may also fail a safety test such as by metal detection or X-ray.
Products falling short of specifications must be removed from production lines to prevent failed product from reaching suppliers or the marketplace. Rejecting conveyors are ideal to use in these cases, enabling rejected products to drop onto other conveyors or into bins, also called reject conveyor accumulators, to be taken away. Diverters, pushers and gates may also be used to manipulate product routes.
What Are the Most Popular Conveyor Reject Mechanisms?
Custom Rejecting Conveyor
Product Routing
Rejecting Tail
Safely and Efficiently Remove Product With Dorner’s Reject Systems
Depositing Conveyor Systems
Product sometimes needs to be placed onto another conveyor or a tray in precise rows or columns. A retract conveyor serving as a depositing conveyor can be equipped with sensors to ensure the product is placed exactly where it needs to be, whether in a box or on another conveyor.
Depositing is critical in product routing, increasing throughput and improving repeatable accuracy. By precisely locating product on a tray, conveyor or pallet, other processes can be sped up. The movement and time the next process requires is decreased because product is where it needs to be.
Dorner’s high-speed retracting tail conveyors may be used for applications such as depositing, rejecting, stacking and product routing. Sensors trigger when the retracting tails should retract.
Dorner can manufacture custom depositing systems based on our customers’ product and applications as part of our custom conveyor systems service. In one example, the Dorner team constructed a high-speed retractable conveyor for a business that needed to stack sheets of thin extruded food product. Once product reaches the end of the conveyor, a sensor triggers the tail to retract 3 feet in only 0.6 seconds. This retraction enables product to fall on a cart under the retracting tail.
In addition to sensors, push-buttons and manual retraction may be utilized, depending on our customers’ needs. Retracts can have multiple drop zones and can occur infrequently, as needed or reoccur every few seconds with precision.
Industries That Use Depositing Conveyors
Let’s explore a couple of key industries in which depositing conveyors are widely used.
Food & Sanitary
Our hygienic designed conveyors meet FDA, BISSC and USDA industry regulations. You can be assured that Dorner’s team can create custom engineered conveyor solutions that meet the needs of your facility.
- Are designed for fast and effective sanitation
- Feature custom-designed solutions for unique systems
- Contain three sanitary levels configured to your application
- Clean up two times faster than competing products
- Require less to clean because of Dorner’s hygienic design
- Are built based on Dorner’s commitment to food safety
Manufacturing
Most businesses require truly customized depositing conveyor solutions as opposed to a one-size-fits-all approach. It’s important to understand that most competitors’ products are standard-built and cannot be customized to suit your business’ unique needs.
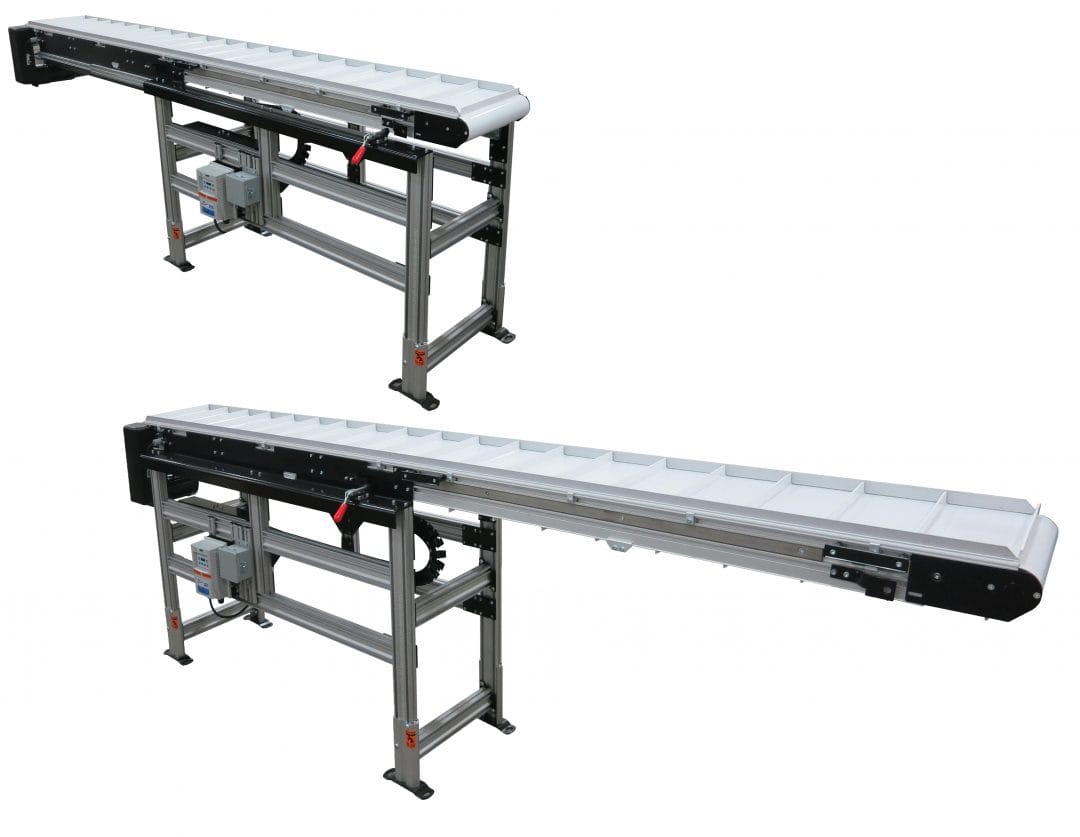